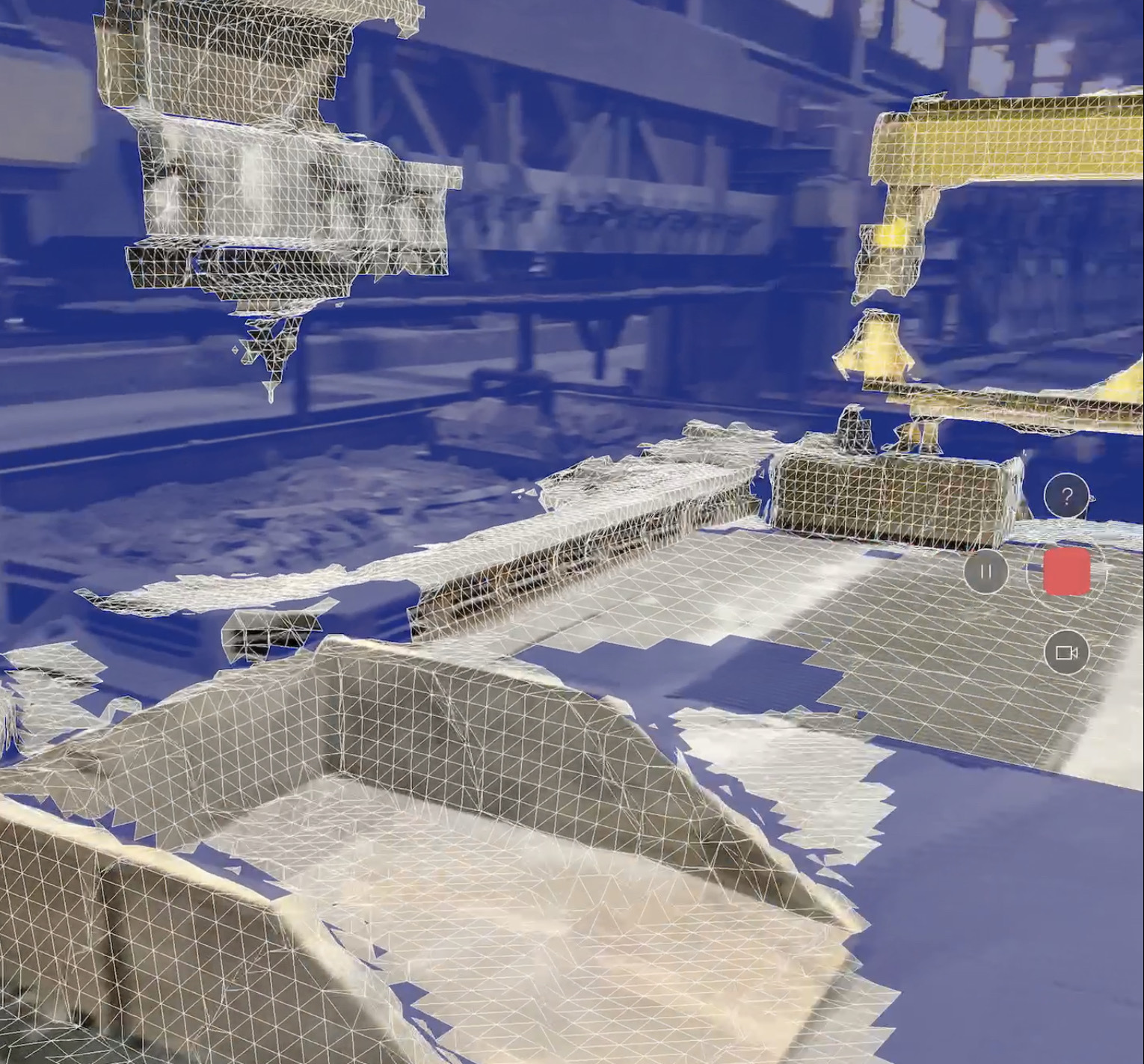
Demystifying the Use of Digital Twins in Industrial Environments
Over the past five years, there has been a four-fold increase in searches for the term digital twin, particularly from countries where manufacturing is a major component of the gross domestic product. Manufacturers of end products have a great interest in digital twins because they can use them to improve efficiency and reduce costs for their operations.
When we look at production processes, we also see a rise in the use of digital twins. Using a digital twin to mirror reality in a digital environment gives us the ability to see processes in a new way and provides the insights to help with decision making.
In an industrial environment, it is important that the digital twin not only considers the data model, but also the relationships between all the different parts of the process. Rather than focusing on building a digital copy of an entire production environment, the value of digital twins for production processes comes from being able to understand, analyse and interact with the different components.
This application of a digital twin can be used to simulate and test different scenarios. By changing different variables in turn, for example increasing the number of mobile robots, we are able to understand the impact on the different components and uncover unforeseen situations. Not only do we get a deeper understanding of current processes, we also see how they can be improved.
—
At Quantillion, we’re specialised in the intralogistics and system integration of autonomous robots in production environments. The installation of our autonomous decision system for mobile robots includes relational interactions with other fixed equipment, human operators, and other processes.